![]() |
Bharat Forge Limited (BHARATFORG.NS): PESTEL Analysis |
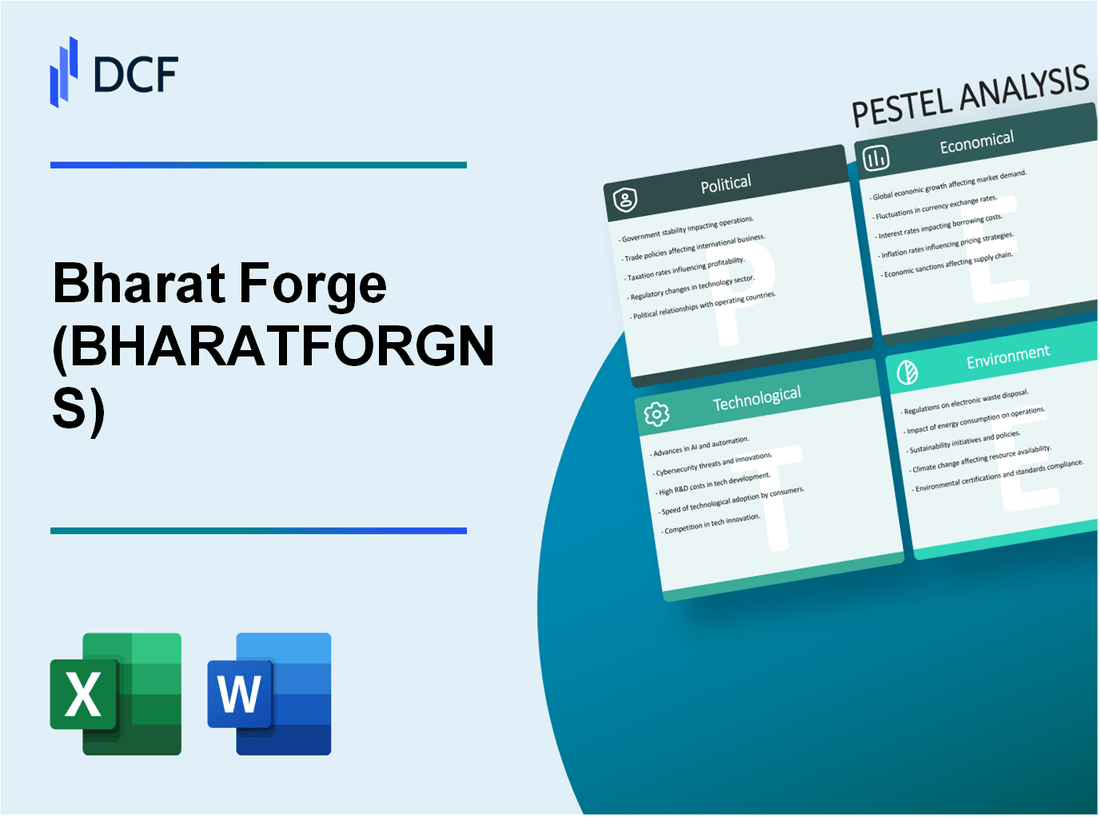
Fully Editable: Tailor To Your Needs In Excel Or Sheets
Professional Design: Trusted, Industry-Standard Templates
Investor-Approved Valuation Models
MAC/PC Compatible, Fully Unlocked
No Expertise Is Needed; Easy To Follow
Bharat Forge Limited (BHARATFORG.NS) Bundle
Bharat Forge Limited, a leader in the manufacturing sector, is navigating a complex landscape influenced by a myriad of factors. From favorable government policies and fluctuating material costs to the pressing demands of sustainability and technological innovation, understanding the PESTLE dynamics at play can provide valuable insights into its business operations and market strategy. Dive deeper to uncover how these elements shape Bharat Forge's future and position in the global market.
Bharat Forge Limited - PESTLE Analysis: Political factors
The political landscape in India significantly impacts Bharat Forge Limited, a leading global provider of forged and machined components for various sectors. The following factors play a crucial role in shaping its business environment.
Government policies supporting manufacturing
The "Make in India" initiative, launched in 2014, emphasizes boosting domestic manufacturing and attracting foreign investment. The manufacturing sector was targeted to contribute 25% to India's GDP by 2025. The government increased the Production Linked Incentive (PLI) scheme allocation to approximately ₹2 trillion ($26 billion) to enhance manufacturing output.
Trade relations impacting exports
Bharat Forge has benefited from India's efforts to strengthen trade relations, particularly with the United States and European Union. India's exports of engineering goods, including components from Bharat Forge, were valued at around ₹800 billion ($10.7 billion) in FY 2022-23. The ongoing negotiations for Free Trade Agreements (FTAs) with various countries are anticipated to further impact export levels positively.
Political stability in key markets
Bharat Forge operates globally, with significant operations in Europe and North America. As of 2023, the political landscape in these regions remains stable, with Germany experiencing a slight GDP growth of 1.2% in 2022 and the U.S. showing a GDP growth rate of 2.1% in Q1 2023. Political stability encourages investment and long-term contracts, essential for Bharat Forge's growth.
Regulatory framework for defense sector
As a supplier to the defense sector, Bharat Forge benefits from favorable government policies. In 2021, India raised the Foreign Direct Investment (FDI) limit in defense manufacturing to 74%. In FY 2023, government defense spending was projected to reach about ₹5.25 trillion ($68 billion), enhancing opportunities for Bharat Forge in defense-related contracts.
Factor | Data/Impact |
---|---|
Government Manufacturing Support | Make in India Initiative targets 25% of GDP from manufacturing by 2025. PLI Scheme allocation at ₹2 trillion ($26 billion). |
Exports and Trade Relations | Engineering goods exports valued at ₹800 billion ($10.7 billion) in FY 2022-23. Ongoing FTA negotiations expected to boost exports. |
Political Stability | Germany's GDP growth rate at 1.2% (2022), U.S. GDP growth rate at 2.1% (Q1 2023). |
Defense Sector Regulations | FDI in defense raised to 74%. FY 2023 defense spending projected at ₹5.25 trillion ($68 billion). |
Bharat Forge Limited - PESTLE Analysis: Economic factors
Bharat Forge Limited operates in a capital-intensive sector heavily influenced by various economic factors. Key economic elements impacting the company's performance include fluctuations in steel and raw material prices, exchange rate volatility, global economic conditions, and interest rate changes.
Fluctuations in steel and raw material prices
The price of steel, a primary raw material for Bharat Forge, has shown significant volatility in recent years. As of Q2 2023, average steel prices in India were recorded at approximately INR 52,000 per ton, reflecting a 15% increase compared to the previous year. This surge is attributed to supply chain disruptions and rising global demand. The cost of other raw materials, such as aluminum and copper, has also fluctuated, with copper prices averaging around INR 800 per kg in 2023, indicating a 20% year-on-year increase.
Exchange rate volatility affecting revenues
Bharat Forge's revenues are significantly affected by exchange rate fluctuations, given its substantial export operations. As of October 2023, the exchange rate of the Indian Rupee against the US Dollar stood at INR 83, down from INR 75 in 2021. This depreciation has impacted earnings, as approximately 30% of Bharat Forge's revenue comes from international markets. In FY 2023, the company reported a foreign exchange loss of around INR 135 million, significantly affecting overall profitability.
Global economic conditions influencing demand
The global economic landscape has been tumultuous, influenced by factors such as ongoing geopolitical tensions and inflationary pressures. In 2023, the International Monetary Fund (IMF) projected global economic growth at 3%, down from 6% in 2021. This slowdown has negatively impacted demand for commercial vehicle components, a primary market for Bharat Forge. The company reported a 10% decline in new orders in Q1 2023 compared to the previous quarter, correlating with the overall reduction in automotive production in key markets like Europe and North America.
Interest rate changes impacting borrowing costs
In response to rising inflation, the Reserve Bank of India raised interest rates to 6.5% in May 2023. This increase has implications for Bharat Forge's borrowing costs, which stood at an average of 9.5% in Q2 2023 for new loans. As of March 2023, Bharat Forge's total outstanding debt was approximately INR 24 billion, with interest expenses amounting to INR 2.3 billion for the fiscal year. These rising costs will place pressure on profitability margins, particularly if revenue growth does not keep pace with financing expenses.
Economic Factor | Data Point | Impact |
---|---|---|
Steel Prices (Q2 2023) | INR 52,000 per ton | +15% YoY increase |
Copper Prices (2023) | INR 800 per kg | +20% YoY increase |
USD/INR Exchange Rate (Oct 2023) | INR 83 | Depreciated from INR 75 (2021) |
Foreign Exchange Loss (FY 2023) | INR 135 million | Affected profitability |
Global Economic Growth (2023) | 3% | Projected down from 6% in 2021 |
Interest Rate (May 2023) | 6.5% | Increase affecting borrowing costs |
Total Outstanding Debt (Mar 2023) | INR 24 billion | Interest expenses of INR 2.3 billion |
Bharat Forge Limited - PESTLE Analysis: Social factors
Bharat Forge Limited, a leading global provider of forged and machined components, has been significantly influenced by various social factors affecting its operations and market positioning. Below are key sociological elements impacting the company's performance.
Workforce skill development initiatives
Bharat Forge has invested substantially in skill development programs. In FY 2022, the company allocated approximately INR 30 crores (around USD 4 million) towards training and development initiatives. This investment is aimed at enhancing the skills of over 5,000 employees across various functions, addressing the skilled labor shortages in the manufacturing sector.
Demographic trends affecting labor availability
India's demographics show a young population, with about 50% of its population under the age of 25. However, the availability of skilled manpower remains a challenge. Bharat Forge is facing increasing competition for skilled labor, both locally and globally, with a projected requirement for over 500,000 skilled technicians in the manufacturing sector by 2025, according to the National Skill Development Corporation (NSDC).
Shift towards electric vehicles impacting product demand
The automotive industry's shift towards electric vehicles (EVs) is reshaping product demand profiles. The Indian electric vehicle market is expected to grow at a CAGR of 43% from 2021 to 2026, potentially affecting Bharat Forge's traditional customer base in the internal combustion engine segment. To adapt, Bharat Forge plans to invest around INR 1,000 crores (approximately USD 135 million) in R&D for developing components suited for EVs by 2025.
Corporate social responsibility expectations
Bharat Forge's commitment to corporate social responsibility (CSR) is reflected in its initiatives in community development, education, and environmental sustainability. The company reported a CSR expenditure of INR 22.5 crores (around USD 3 million) for FY 2021-2022. Key initiatives include:
- Support for over 1,200 students under its scholarship programs.
- Investment in renewable energy projects aimed at reducing carbon footprint by 30% by 2030.
CSR Initiatives | Investment (INR Crores) | Impact |
---|---|---|
Scholarships for students | 10 | 1,200 students supported |
Renewable energy projects | 12.5 | 30% reduction in carbon emissions by 2030 |
Community development | 5 | Improved infrastructure in local villages |
These social factors underline Bharat Forge's strategic positioning and operational challenges as it navigates the evolving landscape of the manufacturing industry in India. The company's proactive approach in addressing these factors demonstrates its commitment to sustainable growth and societal impact.
Bharat Forge Limited - PESTLE Analysis: Technological factors
Bharat Forge Limited, a leading manufacturer in the forging industry, has made significant strides in embracing advanced technological practices that shape its operations and product offerings.
Adoption of Industry 4.0 practices
Bharat Forge has integrated Industry 4.0 technologies, emphasizing the use of connected devices and data analytics to enhance manufacturing processes. In FY2022, the company reported a productivity increase of 20% due to these practices. Investments in smart manufacturing technologies have amounted to over ₹300 crores as of March 2023. The implementation of IoT (Internet of Things) has allowed real-time monitoring of production lines, leading to reduced downtime by 15%.
Research and development in lightweight materials
To address the growing demand for fuel efficiency in automotive applications, Bharat Forge has invested heavily in R&D focusing on lightweight materials. In FY2023, R&D expenditure was reported at ₹150 crores, a notable increase from ₹110 crores in FY2022. The company aims to develop advanced aluminum and composite materials that decrease vehicle weight by 25% while maintaining structural integrity.
Year | R&D Expenditure (₹ crores) | Focus Areas | Weight Reduction Target (%) |
---|---|---|---|
FY2021 | 100 | Lightweight Materials | 20 |
FY2022 | 110 | Lightweight Materials | 22 |
FY2023 | 150 | Advanced Materials | 25 |
Technological partnerships for innovation
Bharat Forge has established key partnerships with technology leaders to foster innovation. In 2023, the company entered into a partnership with Siemens to enhance its digital manufacturing capabilities. This collaboration aims to deploy Siemens’ digital twin technology to optimize production workflows, projected to cut manufacturing costs by 10%. Furthermore, a joint venture with a leading automotive tech company is expected to yield a new range of electric vehicle components, contributing to an expected increase in EV segment revenue by 30% in the next three years.
Investment in automation and AI
The push towards automation is evident in Bharat Forge’s strategy, with substantial investments directed toward AI and robotics. In 2022, Bharat Forge allocated approximately ₹200 crores for automation technologies, including the implementation of robotic process automation (RPA) across its manufacturing units. This investment has resulted in a 25% increase in production efficiency and a 20% reduction in labor costs. The company is aiming for a fully automated production line by 2025, which is expected to further enhance output and product consistency.
Year | Investment in Automation (₹ crores) | Efficiency Increase (%) | Labor Cost Reduction (%) |
---|---|---|---|
2021 | 100 | 10 | 5 |
2022 | 200 | 25 | 20 |
2023 (Projected) | 300 | 35 | 30 |
The technological advancements and investments made by Bharat Forge stabilize its position as a competitive player in the global forging industry, ensuring readiness for the future demands of manufacturing and supply chain efficiency.
Bharat Forge Limited - PESTLE Analysis: Legal factors
Bharat Forge Limited operates in a complex legal environment influenced by various factors that affect its business operations. The following sections detail the key legal factors impacting the company.
Compliance with international trade regulations
Bharat Forge is a significant player in the global automotive and industrial sectors, maintaining exports that accounted for approximately 30% of its total revenue in FY 2022. Compliance with trade regulations has become crucial, especially following the implementation of the Regional Comprehensive Economic Partnership (RCEP), which impacts tariffs and trade flows in Asia-Pacific regions.
Intellectual property rights protection
The company invests heavily in research and development, with an allocated budget of around ₹500 crore for FY 2022-23. Bharat Forge holds numerous patents, with over 200 active patents globally. The protection and enforcement of these intellectual property rights are vital for maintaining competitive advantage, particularly in markets where counterfeit goods pose a significant threat.
Health and safety regulations for manufacturing
Bharat Forge adheres to stringent health and safety regulations, aligning with the Occupational Safety and Health Administration (OSHA) regulations and India's Factories Act, 1948. The company reported a 5% reduction in workplace accidents in FY 2022 due to enhanced safety protocols and training programs, demonstrating commitment to employee safety and regulatory compliance.
Labor laws affecting employment practices
The workforce of Bharat Forge is subject to various labor laws impacting employment practices, including the Industrial Disputes Act and Minimum Wages Act. As of 2022, the company employed approximately 12,000 individuals across its operations. Bharat Forge has also implemented employee welfare programs that exceed legal requirements, contributing to a high retention rate of approximately 85%.
Legal Factor | Description | Impact on Bharat Forge |
---|---|---|
International Trade Regulations | Compliance with tariffs, trade agreements | 30% export revenue reliance |
Intellectual Property Rights | Patent registrations and protection | Over 200 patents held |
Health & Safety Regulations | Compliance with OSHA and local laws | 5% reduction in accidents |
Labor Laws | Minimum wages, employee rights | 12,000 employees, 85% retention rate |
Legal factors play a crucial role in shaping the operational framework for Bharat Forge Limited. Adherence to regulations and proactive measures contribute to the company's resilience and market competitiveness.
Bharat Forge Limited - PESTLE Analysis: Environmental factors
Bharat Forge Limited operates in an industry where environmental factors play a crucial role in regulatory compliance and operational efficiency. The company has been proactive in addressing environmental concerns.
Regulations on emissions and waste management
Bharat Forge adheres to stringent regulations regarding emissions and waste management. In India, the Ministry of Environment, Forest and Climate Change has set regulations that limit particulate matter emissions to 100 mg/Nm³ for manufacturing units. Bharat Forge's manufacturing plants have complied with this requirement, achieving emissions of 60 mg/Nm³ in their Pune facility.
Additionally, the company is committed to waste management practices, where it has implemented a zero landfill policy. In FY 2023, Bharat Forge reported that 95% of its waste material was recycled or reused, exceeding the national average recycling rate of 30%.
Sustainable sourcing of raw materials
The sourcing of raw materials is critical for Bharat Forge's operational sustainability. The company prioritizes sustainable sourcing, ensuring that 70% of its raw materials are procured from suppliers who meet environmental standards. This commitment is reflected in their partnerships with certified suppliers, such as those holding ISO 14001 certification for environmental management.
Energy efficiency initiatives in operations
Bharat Forge has implemented various energy efficiency initiatives aimed at reducing its carbon footprint. The company has enhanced its energy efficiency by 15% over the past two years through measures such as upgrading machinery and optimizing production processes. As of FY 2023, Bharat Forge reported a total energy consumption of 1,500 MWh across its facilities, with renewable energy sources accounting for 20% of this total.
Climate change adaptation strategies
In response to climate change, Bharat Forge has developed adaptation strategies to mitigate risks. The company has invested approximately ₹500 million in the past year to improve infrastructure resilience against extreme weather events. Moreover, it has a target to reduce greenhouse gas emissions by 25% by 2025 as part of its long-term sustainability goals.
Environmental Aspect | Current Performance | Target/Standard | Year |
---|---|---|---|
Particulate Matter Emissions | 60 mg/Nm³ | 100 mg/Nm³ | 2023 |
Waste Recycling Rate | 95% | 30% | 2023 |
Raw Material Sustainability | 70% | N/A | 2023 |
Energy Efficiency Improvement | 15% | N/A | 2023 |
Total Energy Consumption | 1,500 MWh | N/A | 2023 |
Renewable Energy Utilization | 20% | N/A | 2023 |
Investment in Infrastructure Resilience | ₹500 million | N/A | 2023 |
Greenhouse Gas Emission Reduction Target | 25% | N/A | 2025 |
Analyzing Bharat Forge Limited through the PESTLE framework reveals how deeply interconnected external factors shape its strategic direction and operational resilience. With an eye on political support for manufacturing, a dynamic economic landscape, evolving sociological expectations, cutting-edge technological advancements, stringent legal requirements, and pressing environmental considerations, the company is poised to navigate challenges while leveraging opportunities for sustainable growth in the global market.
Disclaimer
All information, articles, and product details provided on this website are for general informational and educational purposes only. We do not claim any ownership over, nor do we intend to infringe upon, any trademarks, copyrights, logos, brand names, or other intellectual property mentioned or depicted on this site. Such intellectual property remains the property of its respective owners, and any references here are made solely for identification or informational purposes, without implying any affiliation, endorsement, or partnership.
We make no representations or warranties, express or implied, regarding the accuracy, completeness, or suitability of any content or products presented. Nothing on this website should be construed as legal, tax, investment, financial, medical, or other professional advice. In addition, no part of this site—including articles or product references—constitutes a solicitation, recommendation, endorsement, advertisement, or offer to buy or sell any securities, franchises, or other financial instruments, particularly in jurisdictions where such activity would be unlawful.
All content is of a general nature and may not address the specific circumstances of any individual or entity. It is not a substitute for professional advice or services. Any actions you take based on the information provided here are strictly at your own risk. You accept full responsibility for any decisions or outcomes arising from your use of this website and agree to release us from any liability in connection with your use of, or reliance upon, the content or products found herein.